The Process
Identifying Opportunities
AMEND completed time studies across all shifts, evaluated TAKT times to study line staffing and balance, reviewed current SOPs, and assessed jobs being completed. After analysis, our team concluded that downtime could be significantly decreased, resulting in higher throughput.
Implementing Change
After evaluation, the AMEND team communicated the need for change in several key areas to to help Patheon overcome operational inefficiencies. AMEND assisted Patheon in implementing procedural changes. designing process maps and communicating them to Patheon's team.
Measuring Results
AMEND developed PowerBI dashboards for Patheon to track real-time metrics such as changeover and downtime. We allowed this company's leaders to leverage all the data and information their programs and machines were already collecting. We made it visible so Patheon's team could make better decisions and drive action.
The Solution
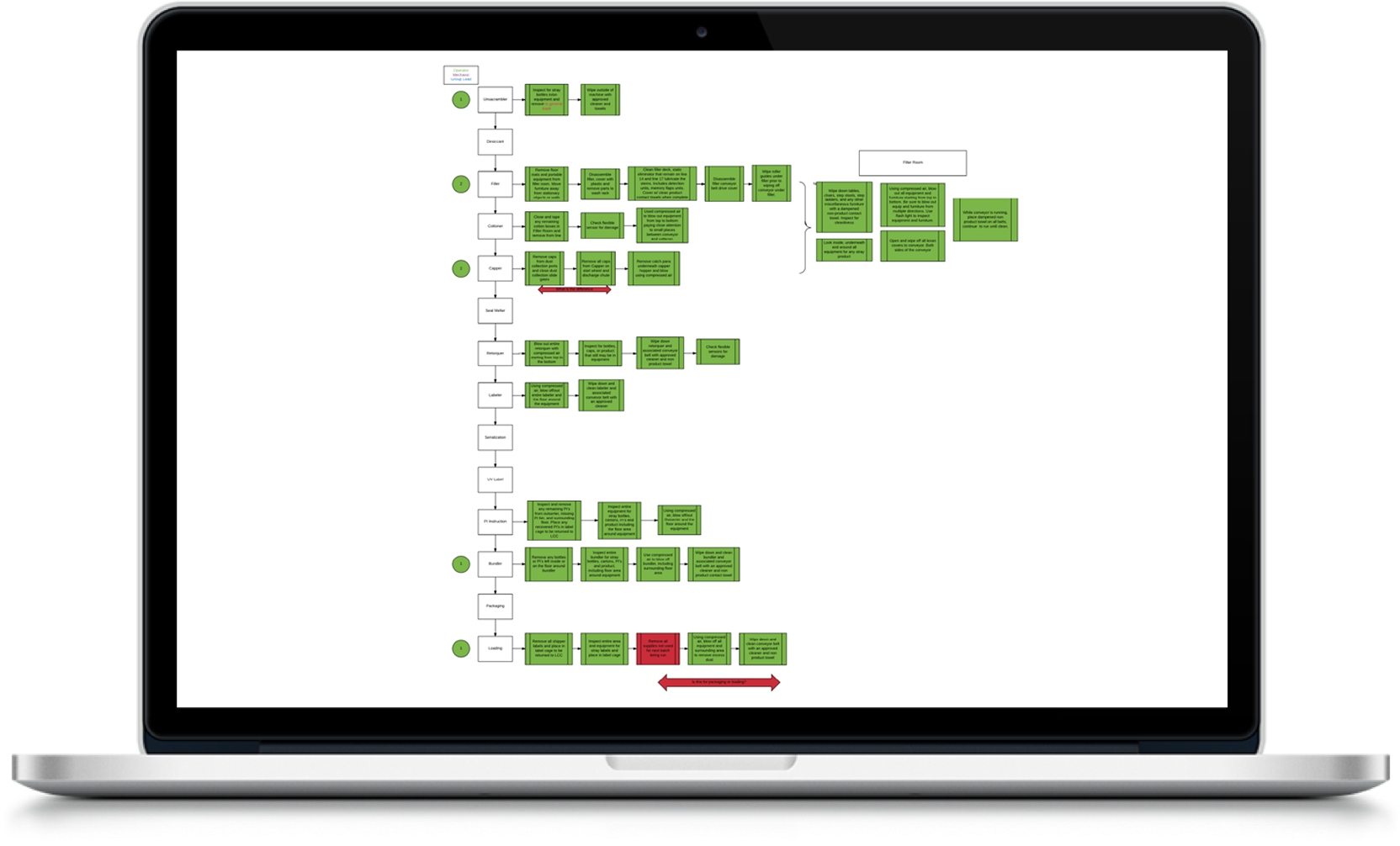
Implemented Better Cleaning Techniques
The AMEND team helped implement a more in-depth and planned cleaning schedule and procedure which resulting in decreased downtime. To do this, AMEND created a “one-pager” for the Patheon's team and for the different zones around the plant.
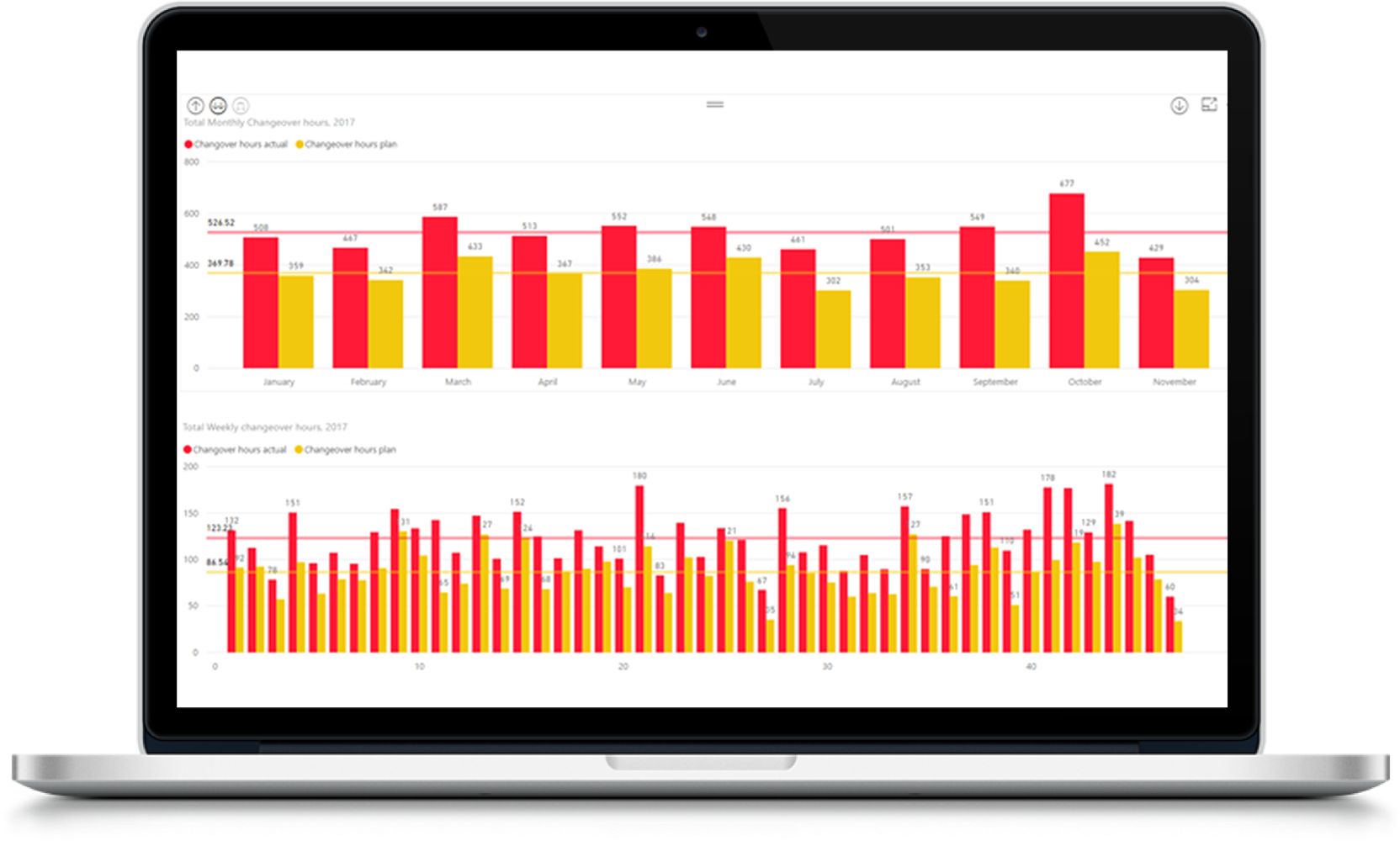
Provided More Visibility to Production
The AMEND team provided Patheon with better visibility into the operations of the plant. This was done through data collection (time studies, process mapping, and on-site data collection) and the utilization of Business Intelligence.
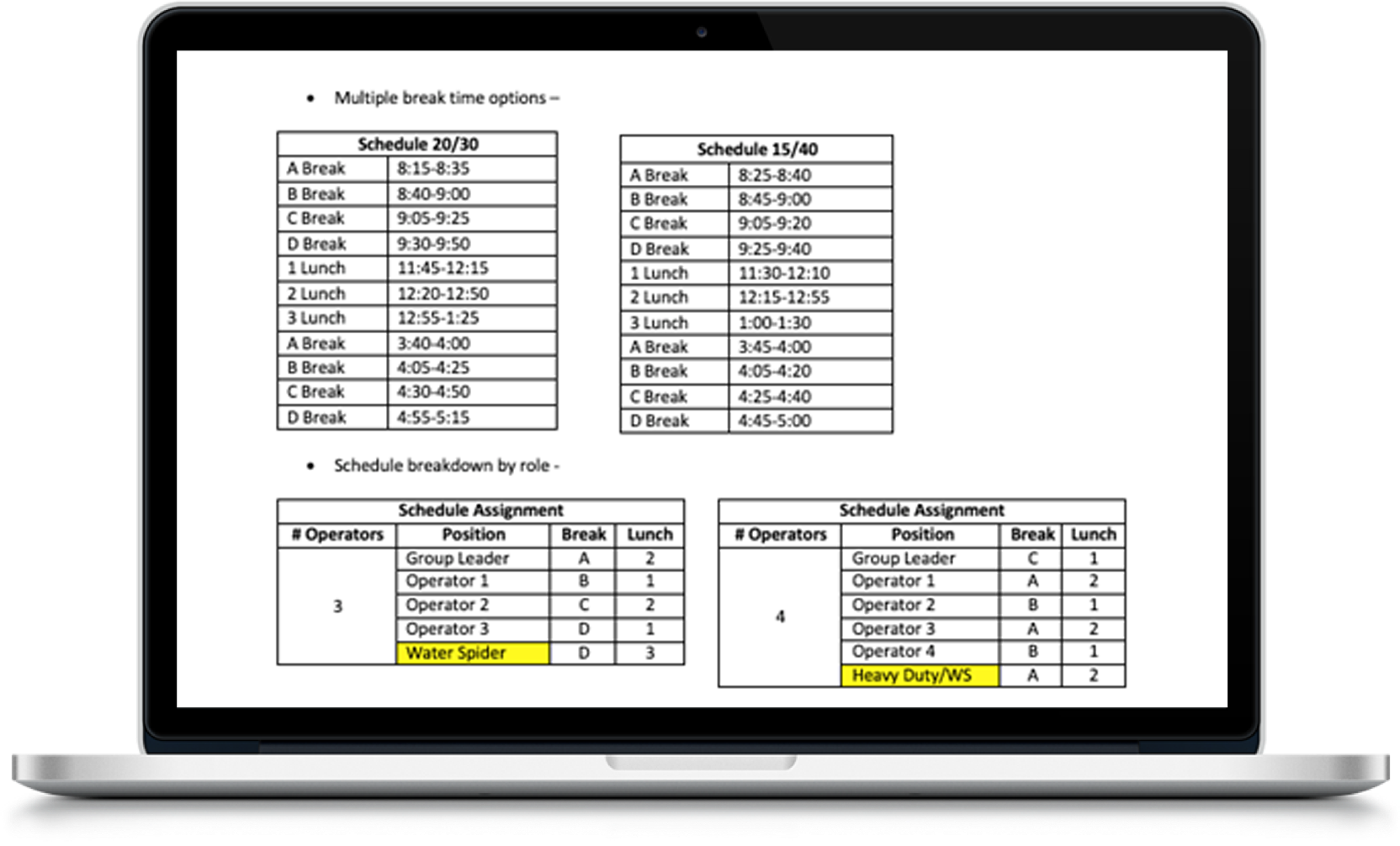
Rearranged Lunch and Break Schedules to Decrease Downtime
By rearranging the schedule for lunches and breaks allowed the lines to run continuously. Before this implementation, the line had to be shut down for breaks and lunches; this took a considerable amount of time due to pharmaceutical policies and restrictions.